OBJECTIVE:
Isotope Innovation
SHINE Technologies encountered several challenges in the development and commercialization of their fusion technology for medical isotope production, particularly lutetium-177 (Lu-177). There was a need to establish a facility capable of meeting the increasing demand for medical isotopes, specifically Lu-177, used in targeted cancer therapies. The initial annual production capacity needed to be achieved with plans for potential expansion.
Given the nature of the production involving radioactive materials, ensuring safety standards and implementing advanced technology for handling these materials were critical. The facility had to integrate cutting-edge safety measures to protect both workers and the surrounding environment.
SHINE aimed to be the first vertically integrated supplier of Lu-177, emphasizing the need for strategic planning and a comprehensive approach to ensure the seamless production and supply of the medical isotope. The company had aspirations beyond medical isotope production, planning to extend fusion technology to address energy challenges by recycling nuclear waste. This required a phased approach and strategic design to harness fusion power for clean and abundant energy.
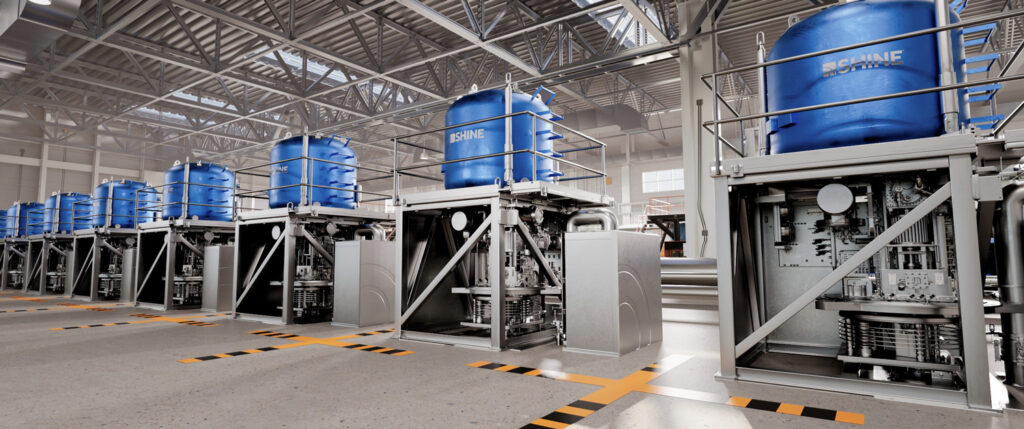
SOLUTION:
Holistic Solutions
Strang’s expertise in architectural and engineering design played a pivotal role in addressing and resolving the challenges highlighted earlier. Leading the way, Strang successfully tackled various issues within the recently completed facility, aligning it with cGMP protocols, utility requirements, and downstream staging of radioactive waste. Our team implemented numerous adjustments to optimize the production facility specifically for medical isotope development.
The facility’s enhancements were strategically focused on ensuring compliance with cGMP standards, prioritizing the safety of the staff, and safeguarding the integrity of the product. Notable improvements included the integration of redundant utilities, such as air handling systems, and the incorporation of ‘long and short’ term decay storage rooms.
Given the intricate nature of radio medicine production, the project necessitated the meticulous development of process flow diagrams. Engaging in detailed discussions, the project team identified additional areas within the facility requiring modifications. These changes were instrumental in enhancing overall safety, operational efficiency, and product protection.