Rapid Advancement Calls for Industry Adaptation
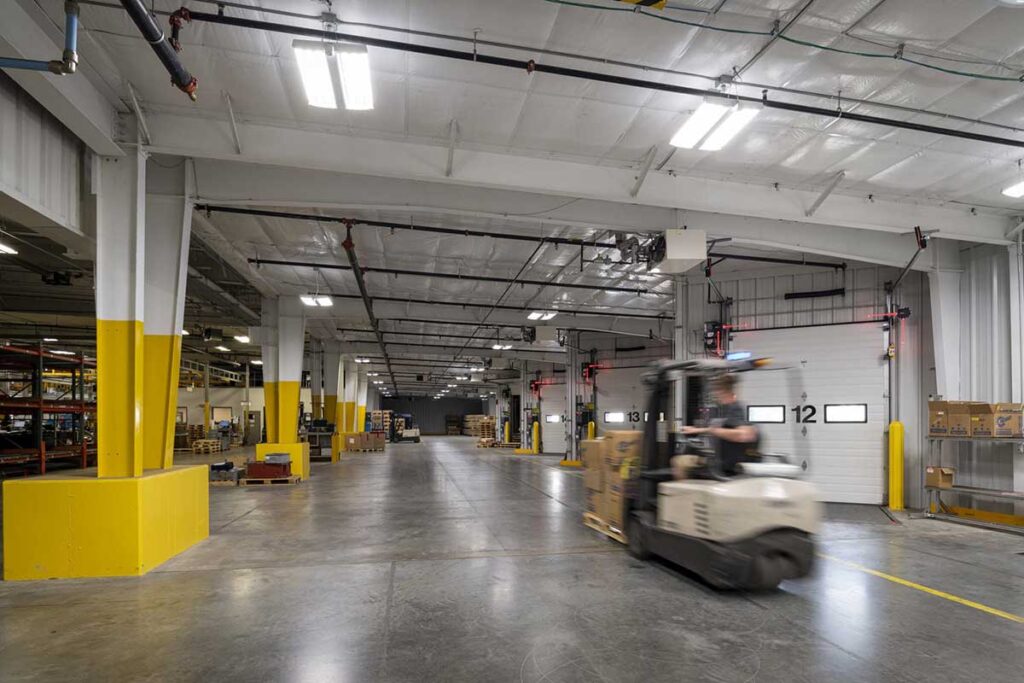
Manufacturing and warehouse facilities – the actual buildings and spaces themselves – have a significant impact on the manufacturing process and ultimately, your bottom line. What was once, “out back” is now front and center as these spaces lead the way in technological advancements, galvanize competitive advantages, and even strengthen your brand’s identity and value.
Of course, when it comes to tech advances in manufacturing, there is a spectrum of need here. Some organizations were early adopters that were quick to envision, then execute this transformation in advanced manufacturing processes. Others required a more deliberate pace to assess their needs. Either way, one thing is certain; manufacturing and aligned warehousing will continue to evolve as integrated strategic partners, thus helping to ensure your organization’s success.
ATTITUDES, APTITUDES, AND APPROACH
“Game changing”. “Cutting edge”. “Pushing the envelope”. These phrases are becoming more and more prevalent in discussions with the manufacturing leaders of today. So, what exactly are these horizon-focused leaders referring to? From lean, advanced, and adaptive digital manufacturing practices to state-of-the-art material handling equipment and high-density warehousing and supply/value chain management, the size, shape, and scope of agile manufacturing is shifting across countless industries. Indeed, the scale of change is seismic, and consequently, the pace is warp speed. This is a strategic response, planned to give organizations a competitive advantage by bringing buyer-focused product(s) to market faster, better, and with designed-in value from creator to customer alike.
Reimagine Your Pathway Towards The Optimal Manufacturing Setting
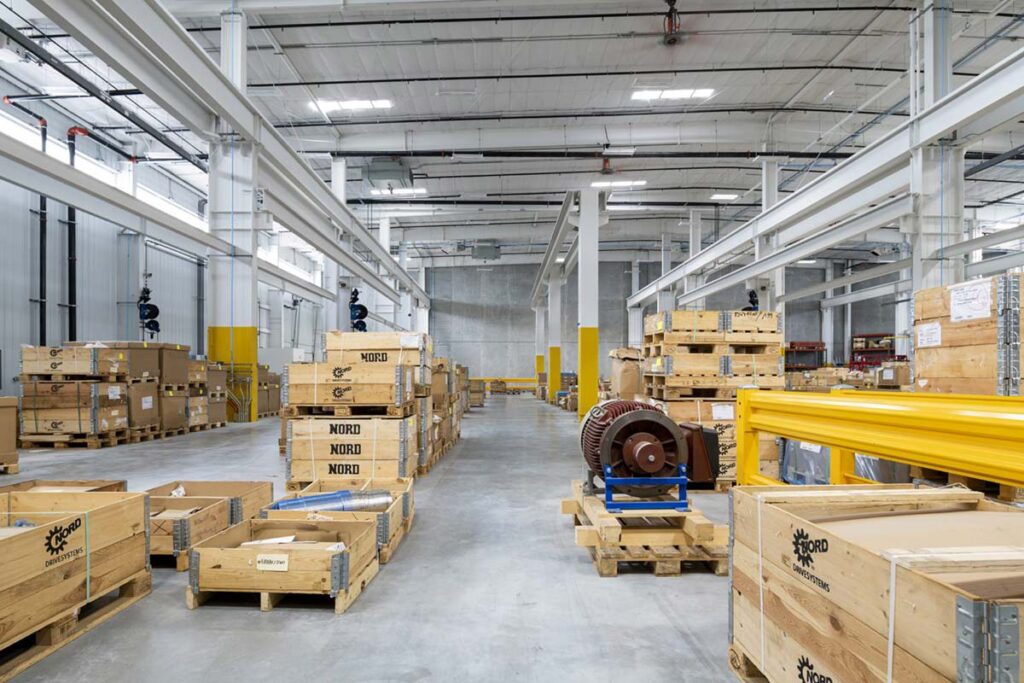
Also consider a very recent and important design dimension; we must be ever-cognizant of the health and safety consequences of COVID-19 within manufacturing and warehousing settings. Space layouts with regards to vicinity of coworkers will require establishing, then meeting exacting building design specifications. How will COVID-19 impact your existing equipment, future automation, or robotics plans? We can almost guarantee this pandemic will have immediate and significant influence upon your floor layouts and corresponding productivity and throughput. Together, we can help guide your COVID-19 safety practices and their resultant impact across your organization.
HOW BUILT ENVIRONMENTS SHAPE MAKING, WAREHOUSING AND DISTRIBUTION
The physical space – the shop floor, assembly areas and warehousing environs – have tangible economic impacts on manufacturing performance and ultimately, an organization’s operating margins. Outdated, non-flexible facilities can adversely impact production planning, compromise project and cost management along with marginalizing asset utilization, mitigate product design innovations, and wreak havoc on productivity and throughput across multiple levels.
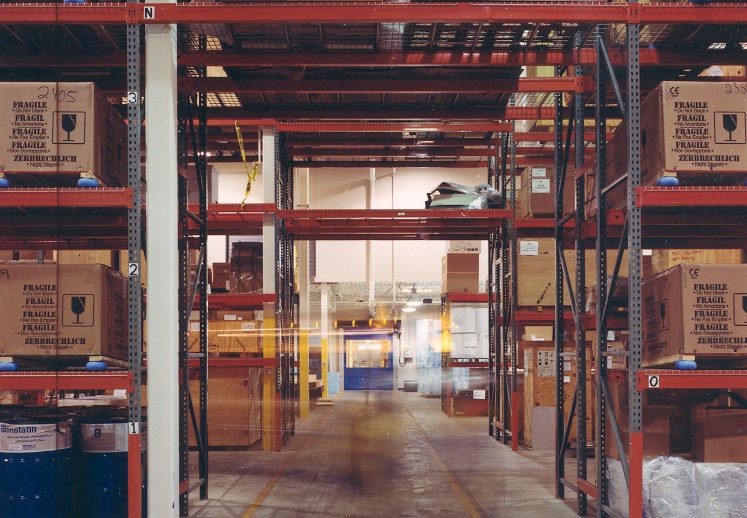
INTEGRATED ENGINEERED SYSTEMS
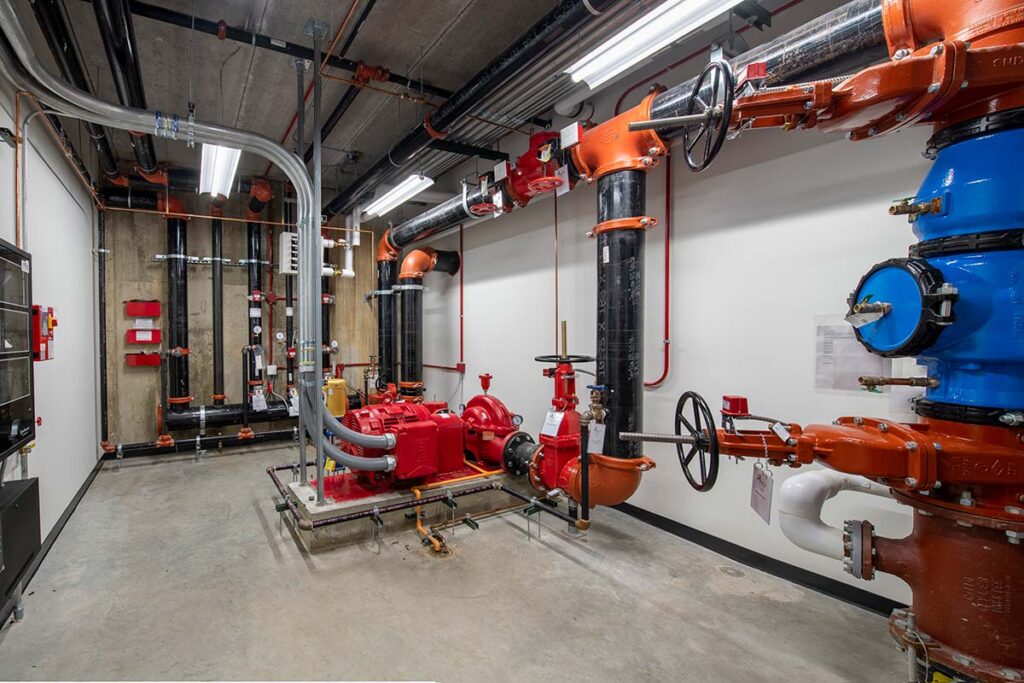
For one, your building’s engineered systems must be integrated, aligned, and highly adaptable to change and to each other. Even seemingly small changes to your floor layouts would mean you will need to rethink relocating support systems i.e. electrical, HVAC, plumbing, IT, and low voltage systems. Compatibility, connectivity, and cooperation amongst these systems is so critical. These systems need to be carefully integrated to avoid conflict with the installation and use of the manufacturing systems. Clearance for cranes, manufacturing power, centralized gas, or air system distribution must work in partnership.
ROI, i.e. Lifecycle, Initial Purchase And Maintenance Cost Analysis Must Also Be Considered
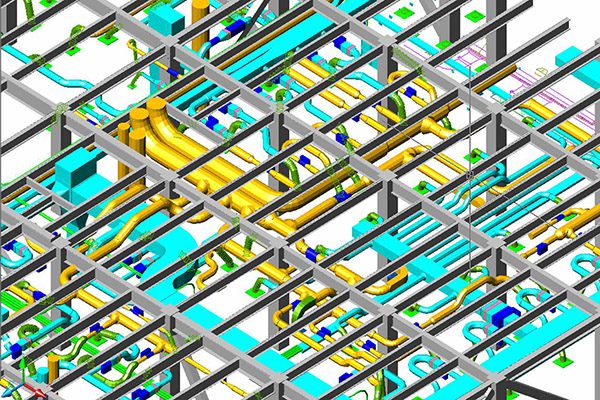

OTHER KEY CONSIDERATIONS
Additional crucial elements of manufacturing building design to consider include the actual plant floors, noise levels, material handling, and lean manufacturing.
- Plant floors must be flatter than ever. Advanced manufacturing oftentimes requires achieving exacting specs, predicated upon equipment operating upon surfaces that meet stringent level tolerance standards. Building design specifications will need to be as precise as the products they produce.
- Noise levels within manufacturing settings can be detrimental to occupant health, safety and ultimately, productivity. There is an increasing number of organizations who desire to go “beyond minimal compliance” of OSHA standard noise levels to achieve optimal employee environments. There exist numerous floor plan layouts, building design considerations, and installed sound absorption/deflection apparatuses which proactively alleviate unwanted or unsafe noise levels. Not surprisingly, industrial noise abatement contributes to employee retention and recruitment – a critical consideration when competition for talent can be fierce.
- Be mindful of advancements in material handling. The manufacturing/assembly/warehousing processing must address operational throughput, minimal space requirement, material flow optimization and distribution. These modernizations will require facilities which function in a multi-dimensional, highly flexible manner where overhead cranes, robotic systems or automated conveyors can adapt to change or be rerouted with minimal disruption to productivity.
- Lean manufacturing practices are reducing warehousing/storage requirements to allow more adaptable/convertible spaces for manufacturing. The remaining warehousing and storage needs will (likely) require much higher vertical density, scalable warehousing, and more automation for retrieval or placement of materials. Combine that with any number of digital systems that map, track, and analyze the movement of your inventory. Each of these factors will overlap and impact one and other. Plan accordingly.
OBSERVATIONS, INSIGHTS, AND SUMMARY
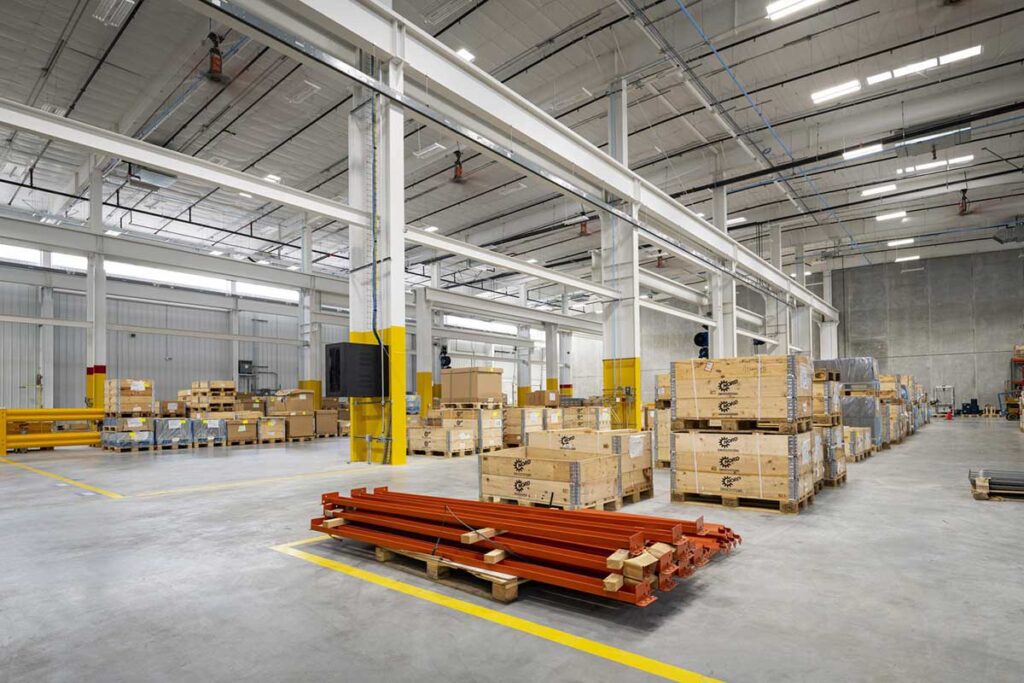
- Cost Control is more important than ever. Stringent monitoring and real-time tracking are required here. Our manufacturing clients’ projects are generally approved with a spending cap. We absolutely must deliver on budget. Therefore, at Strang, we engage several proprietary digital protocols to track and project anticipated expenditures. Such detailed information allows the entire team to make coordinated and integrated fact-based decisions on subjects like budget allocations or payment schedules. Surprises are best left for birthday parties.
- Scheduling is a comprehensive subject which transcends the building alone. Our clients are investing significant capital in advanced manufacturing equipment, packaging machinery, and material handling infrastructure. That equipment set-up and validation process requires time to get operational after the substantial building completion. Moreover, sequential integration of that equipment within the overall schedule requires careful attention to detail. This must occur in simultaneous modus to avoid project cost overruns.
- Quality and design excellence are a must. Indeed, quality within manufacturing can be a very tangible competitive advantage. Because the right built environment is so critical in manufacturing, our clients entrust us with their vision, their budgets, and indeed their future viability as a growing enterprise. We take that responsibility seriously. We strive every day to exceed client expectations and have the people and processes in place to validate and verify all that we do – together. After all, everything we plan for and accomplish will forever be part of our legacies.
- Process is critical for success. Our manufacturing clients are process driven – it’s a good thing, we are too. It takes the right aptitude and discipline to follow a highly collaborative, integrated process strictly and persistently. Ask us about Design Synchronicity™, R.A.D.A.R.© or our dashboard software. Here we apply time-tested facility design and project management protocols that consistently create winning projects.
We have touched upon only several points of consideration for your manufacturing and warehousing facilities. Each of these topics (and more) offer a further wealth of analysis than we have the time to review here. If you would like to discuss further, please let us know. We can be an objective sounding board to help guide your decision-making process.
Written by: