THE PROJECT
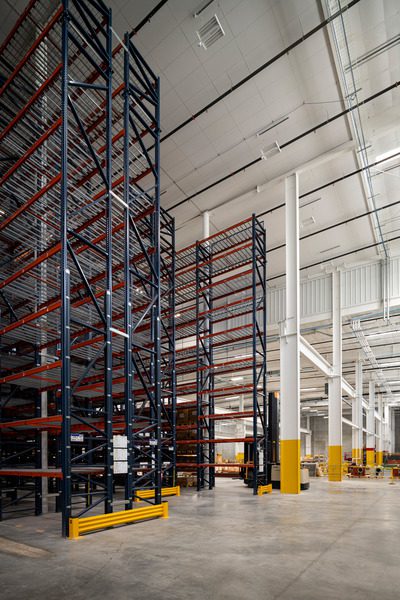
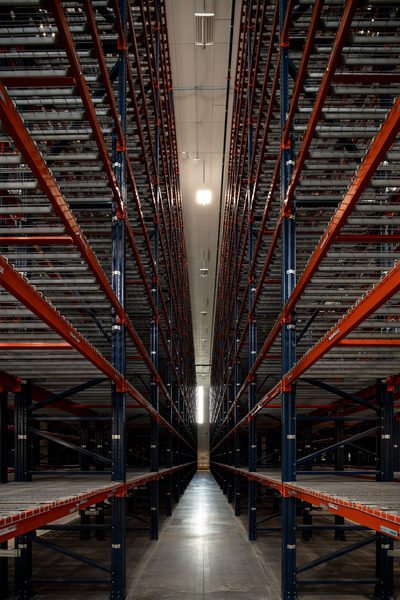
THE SOLUTIONS
A key component of this project is a state-of-the-art overhead material handling system that helps to ensure safe, efficient, and highly productive movement of drive and electronic components throughout the facility.
In addition, this system streamlined the loading and unloading process within the newly designed interior loading dock facility. The newly designed space also added locker rooms, a break room, and a training room to double NORD Gear’s existing capacity.
THE IMPACT
From assembly through prep, to loading for shipping to customers, increased production capacity and reduced production time have been budgeted into NORD Gear’s expanded space. This project not only helped increase NORD Gear’s current manufacturing processes but will accommodate projected growth for the next 10 years.
Efficiency is essential to keep moving forward in manufacturing, and NORD Gear is prepared to drive ahead.
Interested in learning more about manufacturing design? Check out our other related articles below or get in touch. We’d love to hear from you!